Fiberglass Surfboard Laminate Coating Epoxy Resin
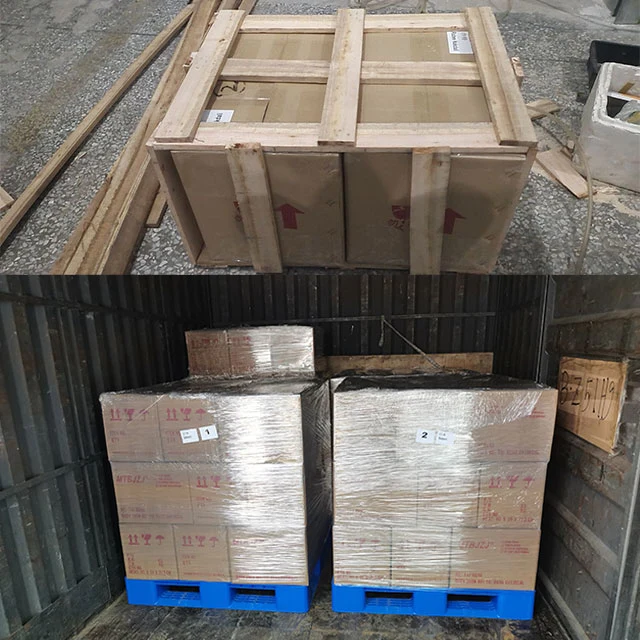
Instruction
Our ALD-4011 Laminating Epoxy Resin and Hardener System is a high quality resin which can be used for a wide range of applications, from fiber-reinforced composites to thin film epoxy coatings,such as fiberglass, carbon fiber, kevlar, or many other types of composite reinforcement. The syrup-like consistency will generate fast wet-out and easy application of any reinforcement.This Epoxy Resin System is 2:1,a low viscosity, clear, low odor epoxy that is not only ideal for layup use, but also as a sealer of porous substrates, such as wood. Because of its penetrating power, it is also excellent for boat repair and general marine repair.
Our ALD-4011 Laminating Epoxy Resin and Hardener System is a high quality resin which can be used for a wide range of applications, from fiber-reinforced composites to thin film epoxy coatings,such as fiberglass, carbon fiber, kevlar, or many other types of composite reinforcement. The syrup-like consistency will generate fast wet-out and easy application of any reinforcement.This Epoxy Resin System is 2:1,a low viscosity, clear, low odor epoxy that is not only ideal for layup use, but also as a sealer of porous substrates, such as wood. Because of its penetrating power, it is also excellent for boat repair and general marine repair.
Features and Benifits of ALD-4011 Laminating Epoxy Resin and Hardener System
• Ultra Clear
• Mixes and blends with Rein Tints and Pigments
• Excellent Adhesion to Polyester Filler Coats
• Solvent Free
• Excellent Clarity
• Rapid Fibre Wet-Out
• Superior UV Stability
• Low Odor
• Room-temperature cure
• Competitive Pricing
• Excellent resistance to yellowing ensure a lighter, stronger, more durable board
• Rapid room-temperature cure for surfboard lamination and cures to a clear, bloom free finish
• Perfect for production laminating and sandwich vacuum techniques
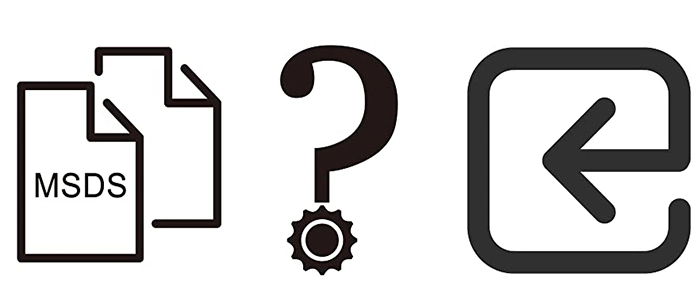
Suggested Uses of Laminating Epoxy Resin and Hardener System
• Brush On Coatings
• Fiber reinforced composites
• Structural Adhesives
Maily be used for a wide range of applications, from fiber-reinforced composites to thin film epoxy coatings,such as Fiberglass composites,Carbon fiber composites,Natural fiber composites,Clear Coatings,Fiberglass boat repair,Adhesives and sealants, Surfboards, stand up paddle boards, hand planes fiberglass, kevlar, or many other types of composite reinforcement. The syrup-like consistency will generate fast wet-out and easy application of any reinforcement.
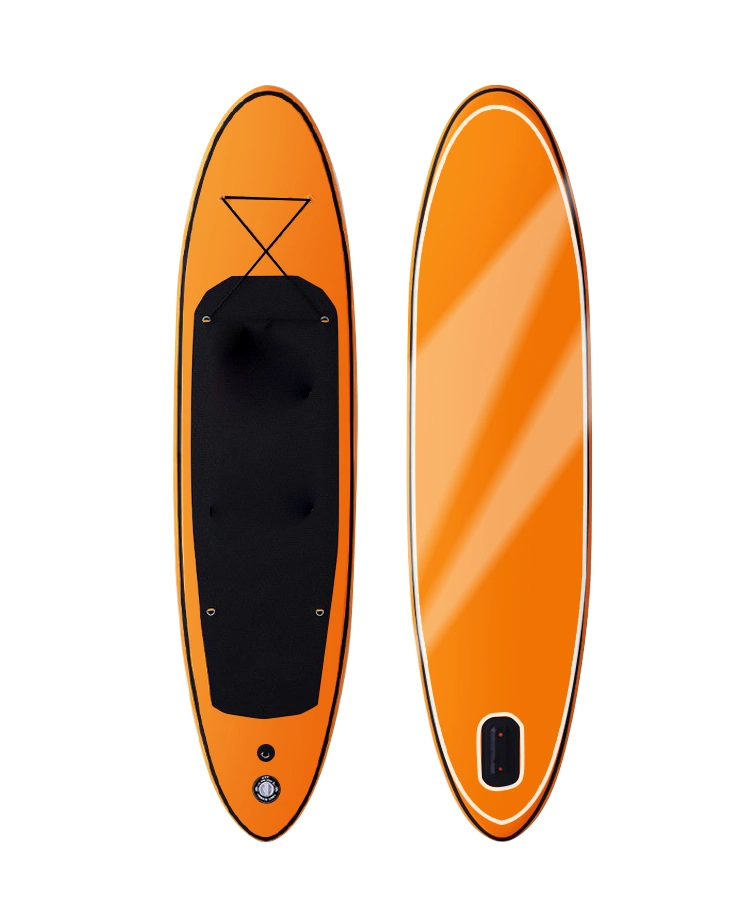
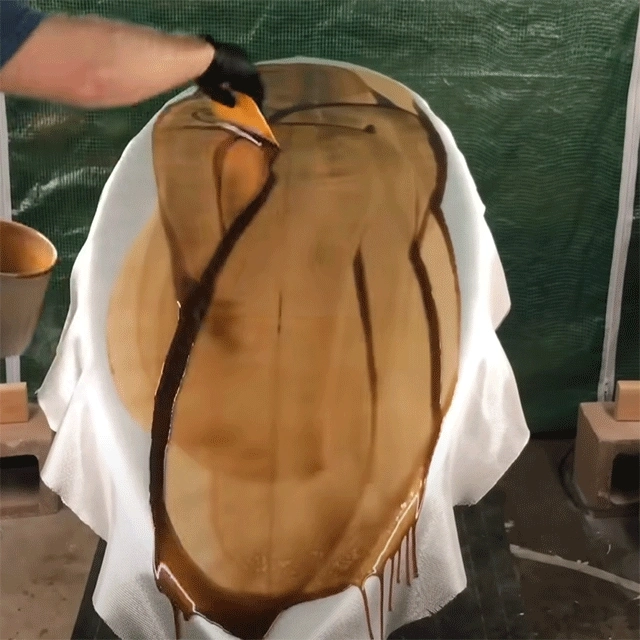
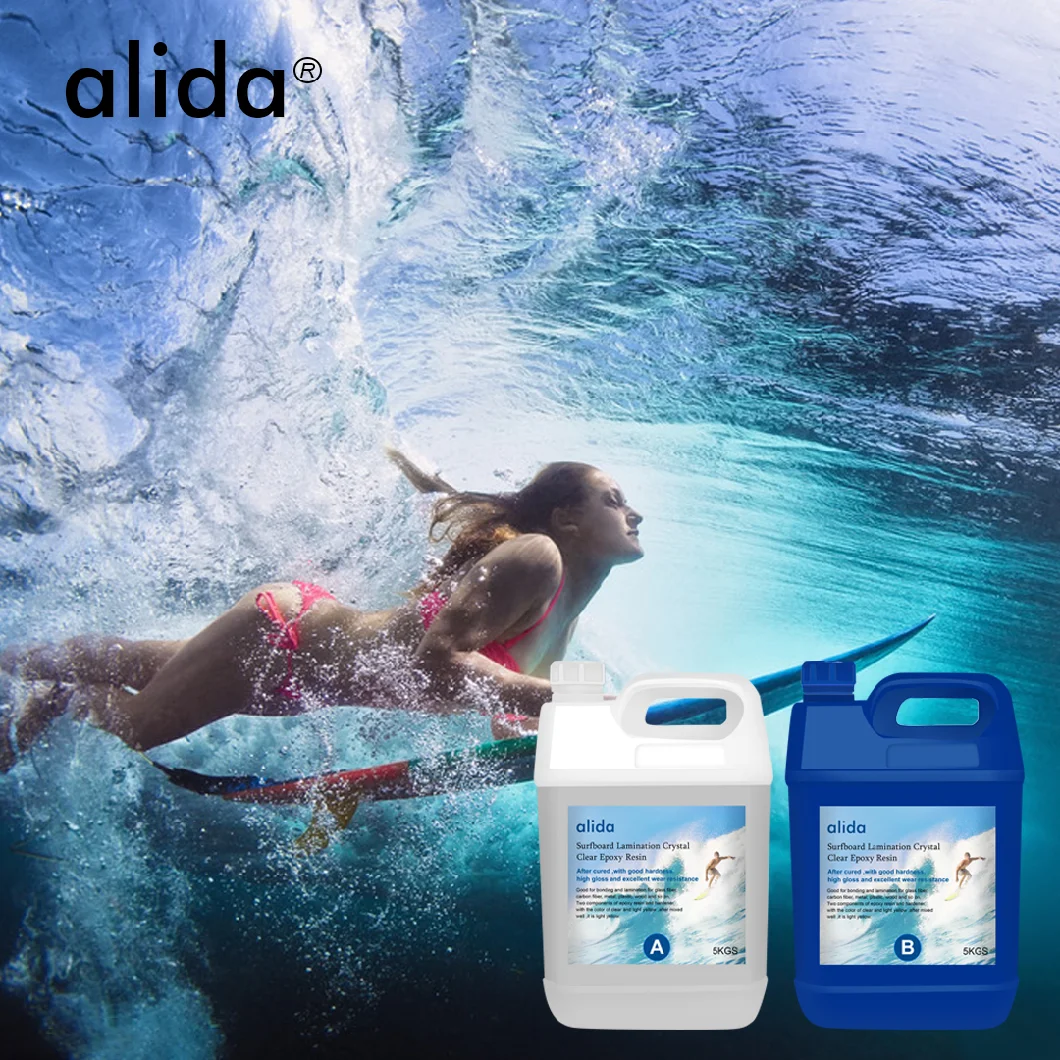
How to use
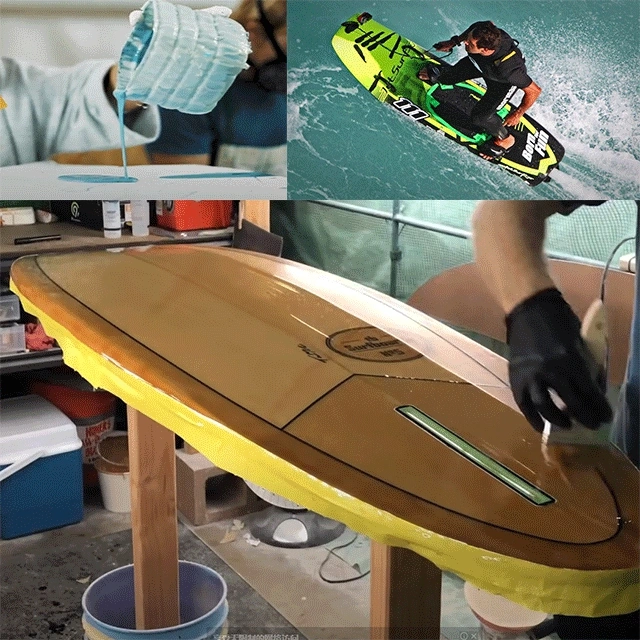
We have various types packages for you choice
---1.5Gal Kit 1gallon resin+0.5gallon hardener
---3Gal Kit 2gallon resin +1gallon hardener
Delivery
---In common ,it takes about 1-3 days to prepare the cargoes for you after you confirm the order.The exact time depends on your quantity.
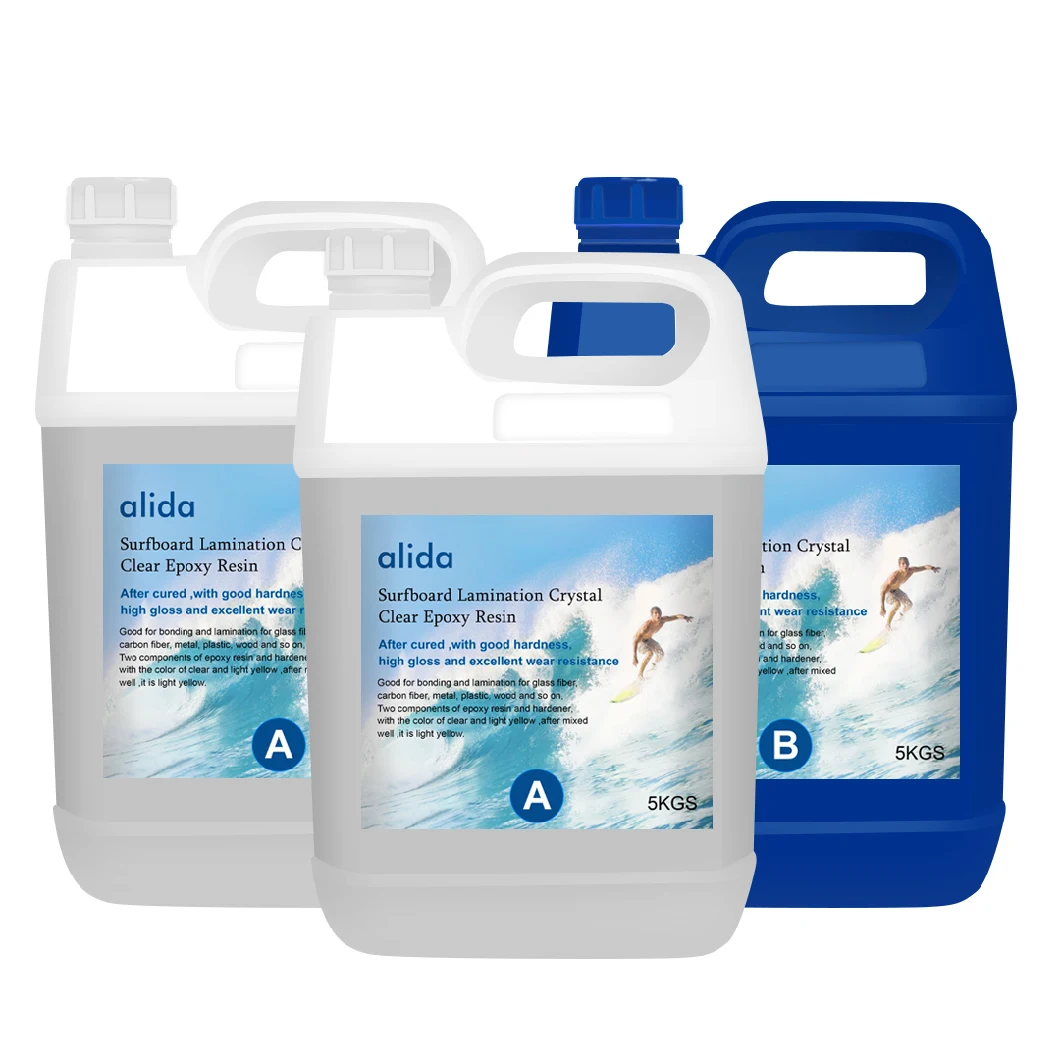
Certification
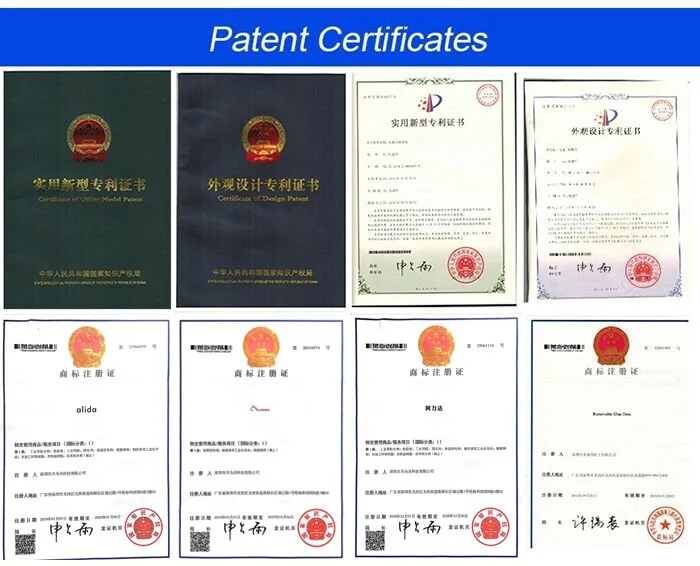
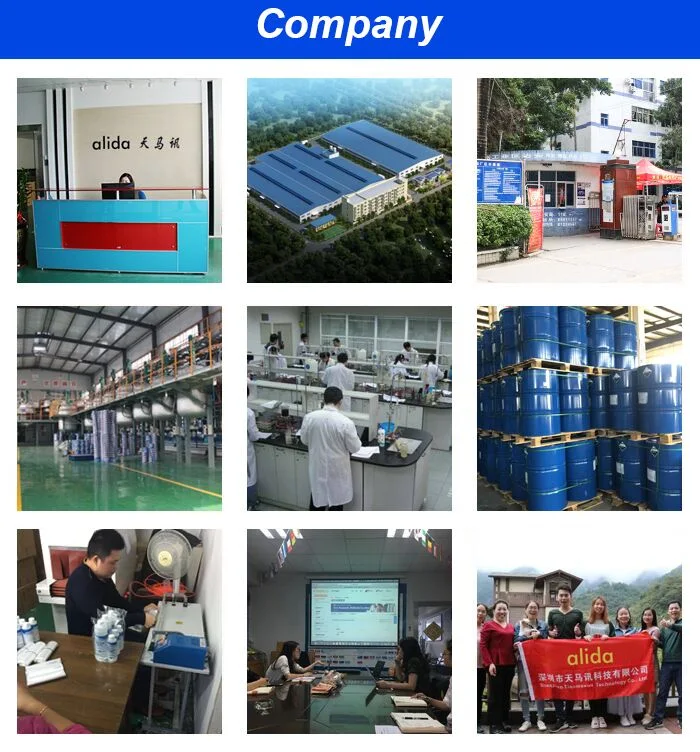
FAQ
1.Q: What's the best way to mix this?
A: You'll want to make sure that you have 2 parts base resin and 1 part curing agent measured precisely, by volume. Pour each into your mixing bucket, and we recommend mixing by hand for at least 3 minutes and between 3-5 minutes or until it is fully mixed. Be careful to scrape the
sides while mixing, but when pouring, do not scrape the sides. This can impart unmixed material that may cling to the side and has not been incorporated. Don't worry about any bubbles in the mixture, they will all work themselves out.
2.Q: How long does it take to cure, and what temperatures can I pourthis in?
A: Our optimum environment temperature range is 72° - 84°F (in a clean, temperature controlled environment. In that temperature range, it will begin to gel in 20-30 minutes, and cure rock hard within 24 hours.Temperatures under 70° will slow the curing process even more, and the closer you get to 60° the curing process will stop. Above 85°, it will begin to accelerate curing, leading to cracking, shrinking and other negative results.
3.Q: Is your epoxy FDA Compliant?
A: The short answer is, yes. Once our epoxy has cured, it becomes safe,per FDA code, 21CFR175.300 which states "Resinous and polymeric coatings may be safely used as the food-contact surface of articlesintended for use in producing, manufacturing, packing, processing,
preparing, treating, packaging, transporting, or holding food" and can be used as a "functional barrier between the food and the substrate".
4.When Can I Demould?
A: Our optimum environment temperature range is 72° - 84°F in a clean temperature controlled environment. In that temperature range, you can demould between 18 and 24 hours, and its optimal workability will be at 24-30 hours. At 30 hours it will sand and plane as easy as wood!